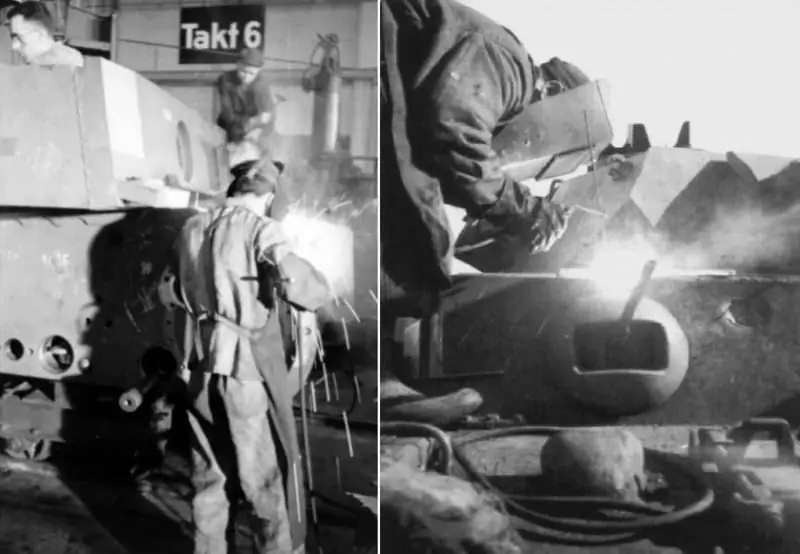
Alman yaklaşımı
Büyük Vatanseverlik Savaşı sırasında kaynak teknolojileri ile ilgili malzemenin ilk bölümünde, Sovyet teknoloji uzmanlarının ve bilim adamlarının ana başarılarından birinin tank gövdelerinin ve kulelerin kaynak otomasyonunun tanıtılması olduğu belirtildi. Nazi Almanya'sında tank fabrikalarında otomatik kaynak kullanılmadı. Bunun çok önemli bir açıklaması vardı - savaşın ana döneminde, Üçüncü Reich'in tank endüstrisi, kaynakçılar da dahil olmak üzere yüksek nitelikli işgücü sıkıntısı yaşamadı. Ve Sovyetler Birliği'nde, doğudaki büyük işletmelerin tahliyesi sırasında, sadece tank montajının kalitesini değil, hatta üretim olasılığını bile tehlikeye atan, endüstri için değerli personel kaybedildi. Almanya'da, "Panterler" ve "Kaplanlar" gövdelerini kaynak yaparken, ayrı dikişlere ayrı kaynakçıların atandığı noktaya geldi! Mühendis V. V. Ardentov, muzaffer 1945 yılında "Tank endüstrisi Bülteni" nde "Almanya'nın zırh kesme ve tank gövdelerinin kaynağı konusundaki deneyimi" materyalinde bunu yazıyor. Çalışması, Kirchmeser ve Brandenburg'daki iki zırhlı gövde fabrikasının çalışmasına dayanıyordu. Açıkçası, bu fabrikalar, savaşın son aylarına kadar ayrı dikişler için ayrı kaynakçılar şeklinde böyle bir teknolojik lüksü karşılayabilirdi.
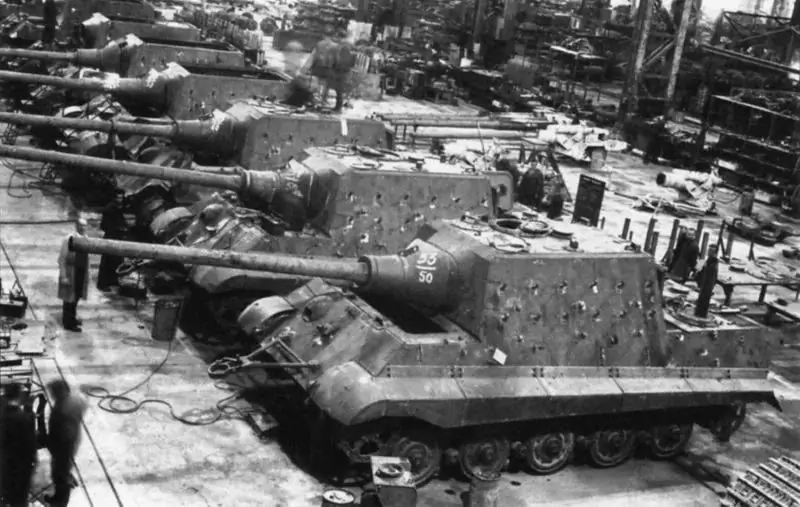
Gövdeleri kaynaklamadan önce, 1942 yılına kadar mekanik olarak gerçekleştirilen zırh plakaları kesildi. Dikenli bağlantılar için zırh plakalarını kesmek için, Sovyet tank endüstrisinde de benzer durumlarda kullanılan asetilen-oksijen kesiminin kullanılması çok daha uygundu. Burada Almanlar, hem verimlilik hem de kesim kalitesi açısından tank üreticilerimizin önündeydi. Bu, büyük ölçüde, zırh plakasının kalınlığına ince ayar yapma kabiliyetine sahip yüksek kaliteli aletlerin (gaz kesme makineleri Messer ve Grisheim) kullanılmasının bir sonucudur. Ayrıca, Almanlar yüksek derecede saflaştırma oksijeni kullandılar -% 99'dan fazla. Son olarak, zırhın kesilmesi sırasında Almanlar, pah kırma da dahil olmak üzere birkaç meşale kullandı. Alevle kesme işleminin kendisi otomatikleştirildi - bu, işlemi hızlandırmayı ve çok daha doğru hale getirmeyi mümkün kıldı.
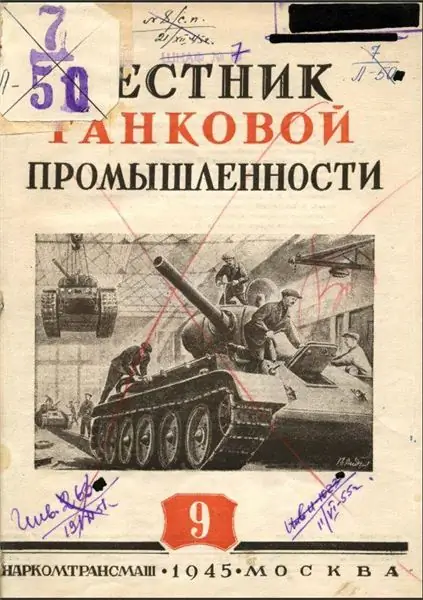
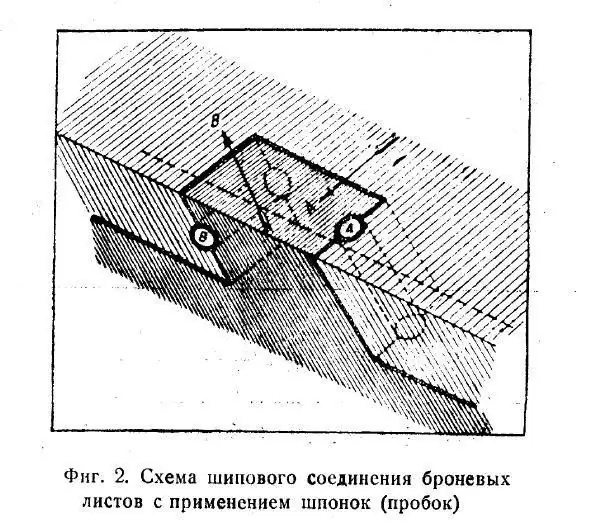
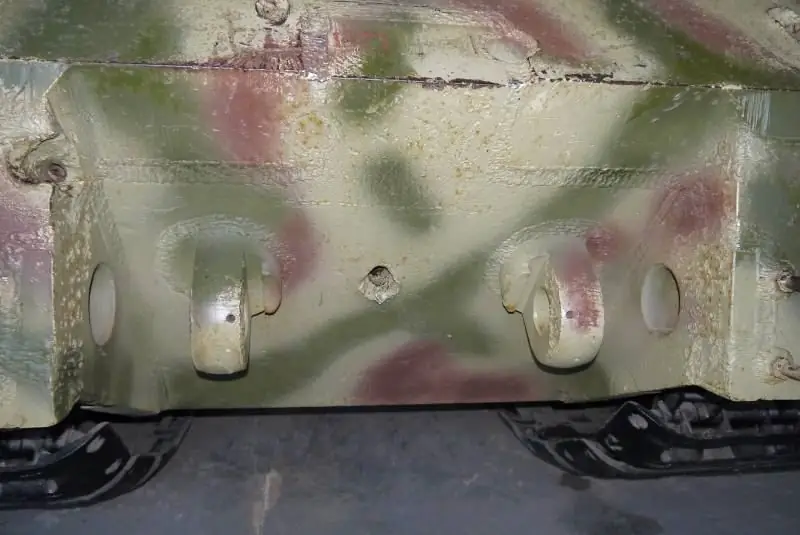
[merkez]
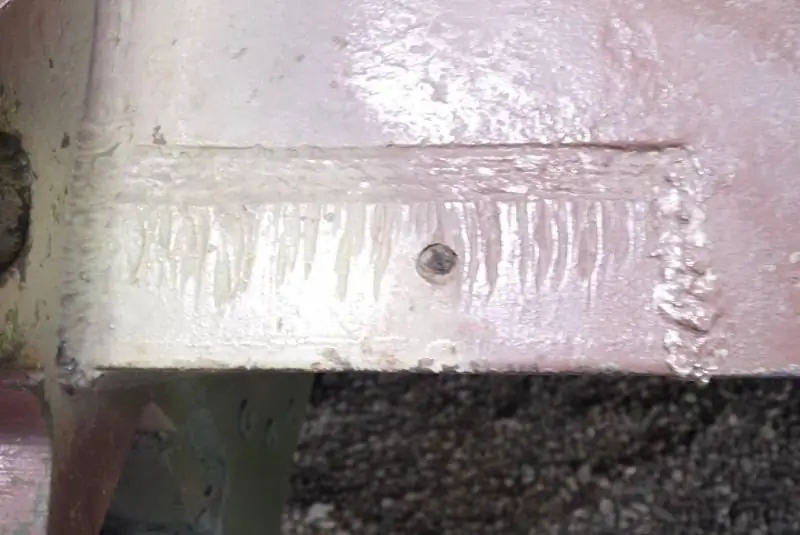
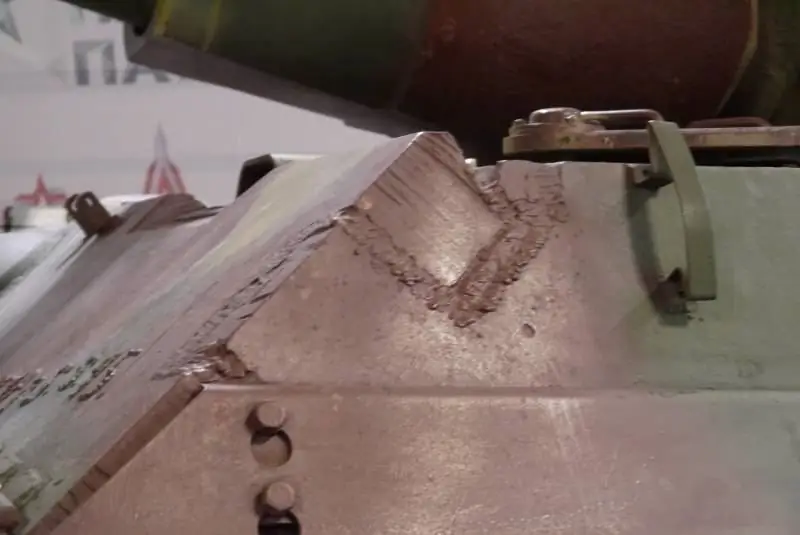
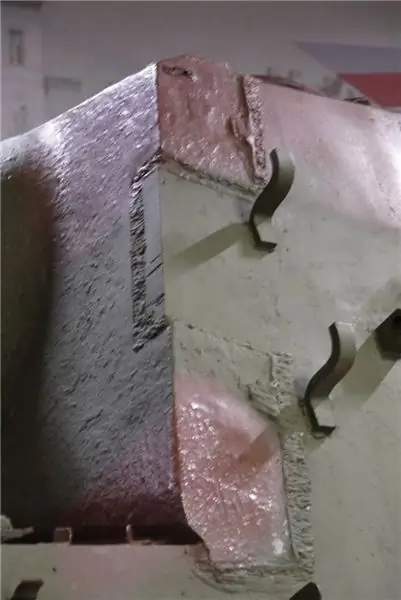
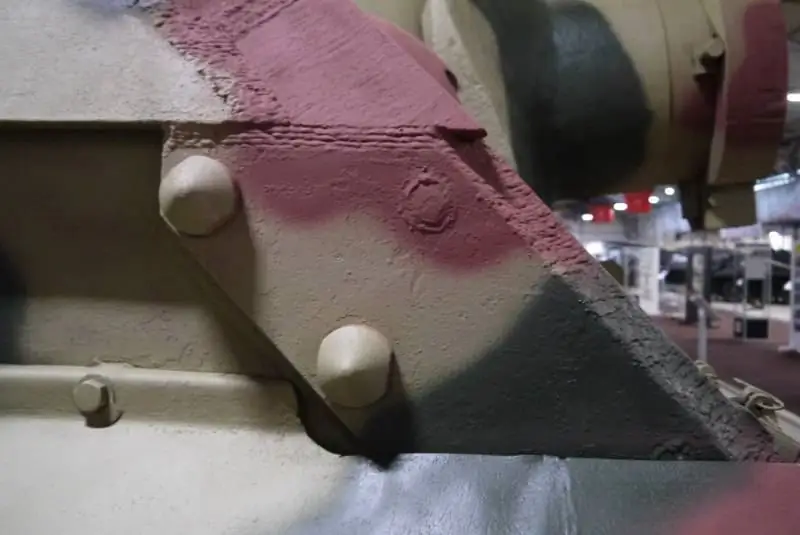
[/merkez]
Bildiğiniz gibi, 1942'den itibaren Alman tanklarının gövdelerinin ayırt edici özelliklerinden biri, zırh plakalarının dikdörtgen veya eğik bir başak ile başak bağlantısıydı. Aynı zamanda, Almanlar basit bir artikülasyonla sınırlı değildi - ayrıca, güç için, eklemlere silindirik anahtarlar veya tapalar yerleştirildi. Özellikle, bu, orta tanklar "Panther", kendinden tahrikli silahlar "Ferdinand", ağır "Kaplanlar" kuleleri ve birkaç "Maus" kolordu üzerinde yaygındı. Bu tapalar, kaynak için monte edildikten sonra birleştirilecek sacların ek yerlerine sokulan, çapı 80 mm'ye kadar olan çelik rulolardı. Tapalar, zırh plakalarının sivri uçlarının kenarlarının düzlemine yerleştirildi - her eklem için bir çift gerekliydi. Aslında, anahtarların takılmasından sonra, kaynaktan önce bile başak bağlantısı tek parça hale geldi. Bu durumda, dübeller zırh ile yüzeyle aynı hizada monte edildi ve tabanın çevresi boyunca kaynaklandı. Tank gövdelerinin zırh plakalarının sivri bağlantısı, hem kaynak dikişlerinin hem de zırhın balistik korumasını belirgin şekilde iyileştirdi. Her şeyden önce, bu, çatlakların yayılmasını bir şekilde azaltan ayrı bölümlerden oluşan kaynağın toplam uzunluğunu artırarak sağlandı.
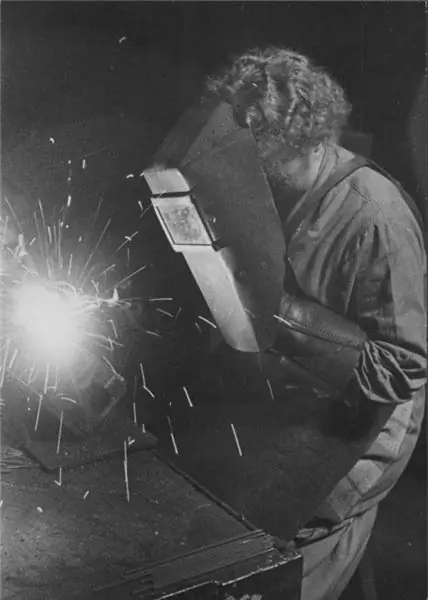
Alman tanklarının gövdelerinin imalatındaki sorunlardan biri, oyukların ve deliklerin imalatıydı (örneğin, yukarıda belirtilen zırh bağlantıları için). Onları gazla kesmek imkansızdı, bu yüzden sondaj kullanıldı. Başlangıçta, yüzey sertleştirme prosedürü uygulanan E-18 ve E-19 kalite çelikler için genellikle uygun bir matkap bulmak imkansızdı, zırhın dış tabakasının çok sert olduğu ortaya çıktı. Söndürmeden önce bir delik açılması durumunda, delik alanında düzensiz bir su verme oluştu, ardından deformasyon ve radyal çatlama oluştu. Evet ve Alman tanklarında çatlaklar vardı ve önemli olanlar ve Almanların bunlardan kaçınma çabaları daha sonra tartışılacak. Kısmen, zırhın delikler alanındaki düzensiz sertleşmesi sorunu, fırına gönderilmeden önce delikleri kapatmak için kullanılan özel bir refrakter macun ile çözüldü. Ancak, yine, bu sorunu yalnızca kısmen çözdü. Sadece 1944'ün sonunda, Essen'deki Elektrotermal Enstitüsünde, bu sorunun zırhın sertleştirilmiş bölgesinde yerel bir tavlama prosedürü ile çözüldü. Almanlar tarafından geliştirilen birim, makalesinde Stalin Ödülü sahibi Teknik Bilimler Adayı A. A. Shmykov tarafından anlatılıyor. Materyal, 1945'in sonunda, zamanı için gizli olan ve bize tanıdık gelen “Tank Sanayi Bülteni” özel baskısında yayınlandı. Savaş sonrası yıllarda, Vestnik'in sayfaları, yeterince ele geçirilen ekipman olduğu için Alman mühendislerin mühendislik hilelerinin ayrıntılı analizi açısından zengindi.
Ancak deliklerin açıldığı zırhın yerel olarak serbest bırakılmasına geri dönelim. Ünitenin temeli, 220 amperlik bir elektrik akımının ve 380 voltluk bir voltajın geçtiği sondaj sahasına bağlı bir grafit elektrottu. Sonuç olarak, zırh tavlama sıcaklığına ısıtıldı. Zırhın kalınlığına ve deliğin çapına bağlı olarak bu, 7 ila 15 dakika arasında sürüyordu. Temperleme işleminden sonra zırhın sertliği 2-2,5 kat azaldı. Yerli endüstrinin (tank endüstrisi dahil) ayrıca akımla ısıtılarak çelik tavlama kullanması dikkat çekicidir - Almanların "know-how"ı sadece bir grafit elektrot kullanımındaydı.
Almanlar ve elektrotlar
Almanlar ayrıca,% 0.40-0.48 aralığında karbon içeriğine sahip yüksek sertlikteki zırhlarının levhalarını kaynak yaparken tatil kullandılar. Bu, metalurji mühendislerinin T-34 zırhındaki çatlamayı azaltmak için tarifler aradığı savaş sırasında TsNII-48 (Zırhlı Enstitü) uzmanları tarafından biliniyordu. Anlaşıldığı üzere, Almanlar zırh plakalarını 500-600 derece (yüksek tatil) sıcaklıklarda serbest bıraktılar ve daha sonra önceden ısıtılmış zırhı birkaç geçişte 150-200 dereceye kaynakladılar. Kaynakçılar, Alman tanklarının zırhının kalınlığı göz önüne alındığında, inanması zor olan 5 mm'den daha büyük elektrotlar kullanmadılar. 4 mm çapında elektrotlar, 120-140 amperlik bir akımda, 5-6 mm - 140-160 amper çapında çalıştı. Bu teknoloji, kaynak alanının aşırı ısınmamasını mümkün kıldı. Bu, daha küçük bir sertleştirme ve tavlama bölgesinin elde edildiği anlamına gelir. Ek olarak, kaynaktan sonra dikiş çok yavaş soğudu - tüm bunlar sonunda Almanların kaynaklı bağlantı yerlerindeki çatlaklarla az çok başarılı bir şekilde başa çıkmasına izin verdi. Ek olarak, östenitik elektrotlar ağırlıklı olarak kullanıldı, bu da kaynağın yüksek sünekliğine ve kırılgan martensitik duruma uzun süreli geçişine yol açtı. TsNII-48 mühendisleri, bu teknikleri T-34'ün üretim döngüsüne başarıyla aktarmayı mümkün kılan tank zırh kaynağının teknolojik döngüsünün özelliklerini çok dikkatli bir şekilde incelediler. Doğal olarak, tank endüstrisindeki hiç kimse tank gövdesi boyunca bu kadar zahmetli çok katmanlı kaynak dikişi uygulamasını karşılayamazdı, Alman "know-how" sadece çatlamaya eğilimli en kritik dikişlerde kullanıldı.
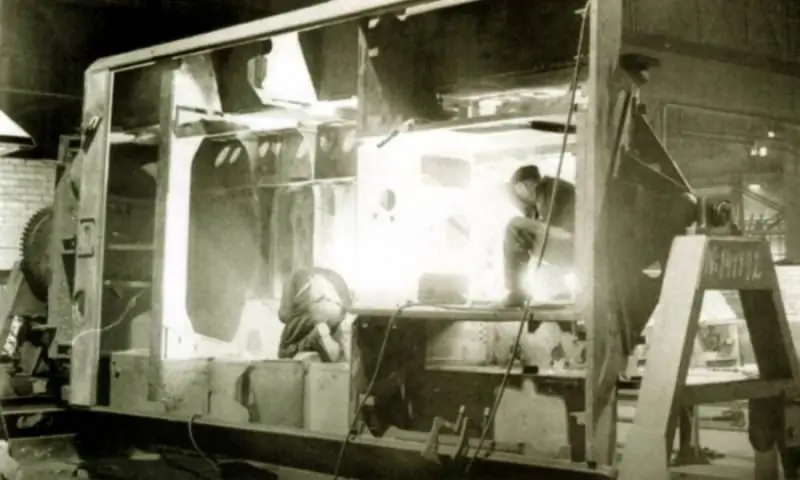
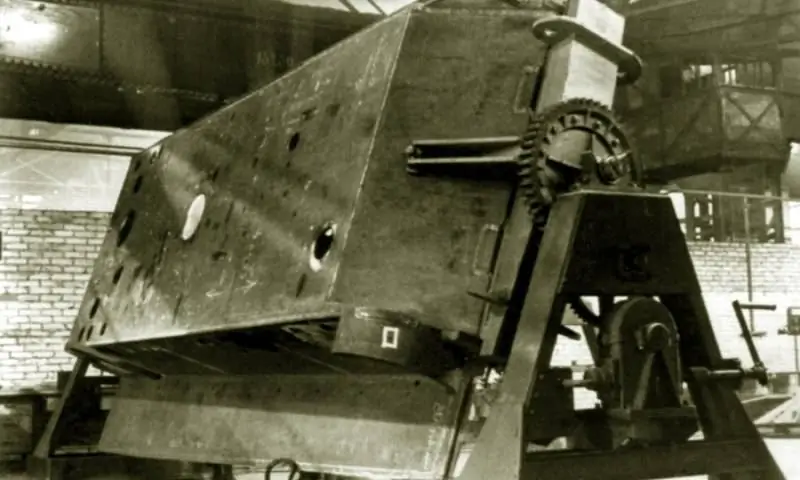
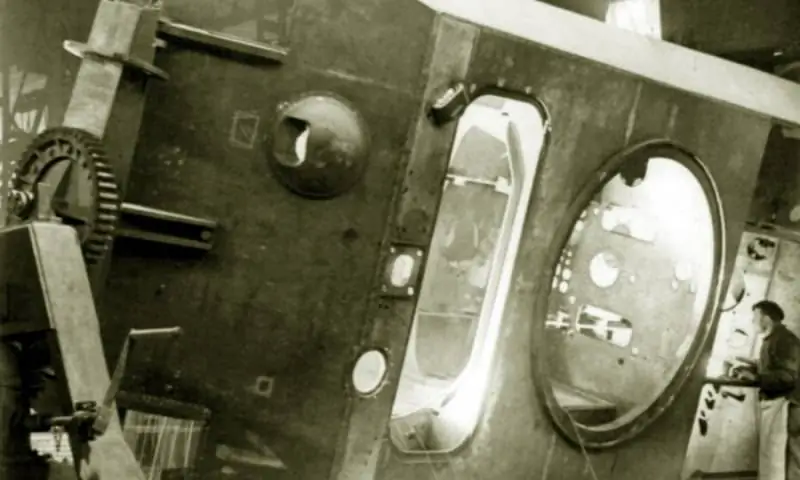
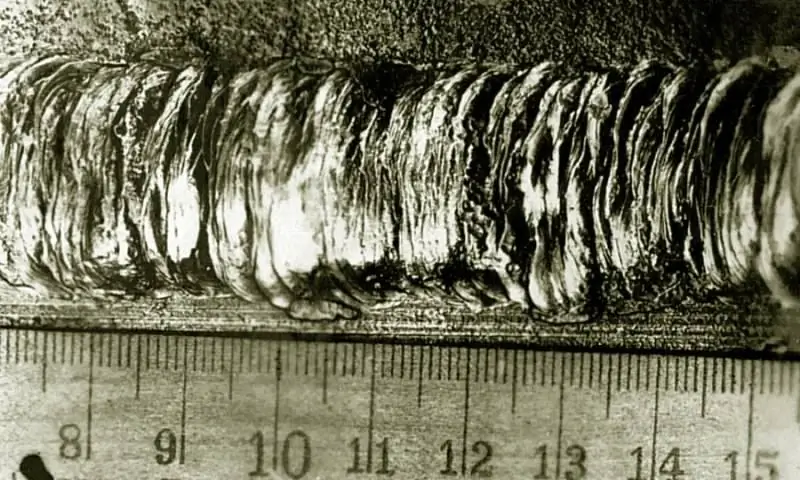
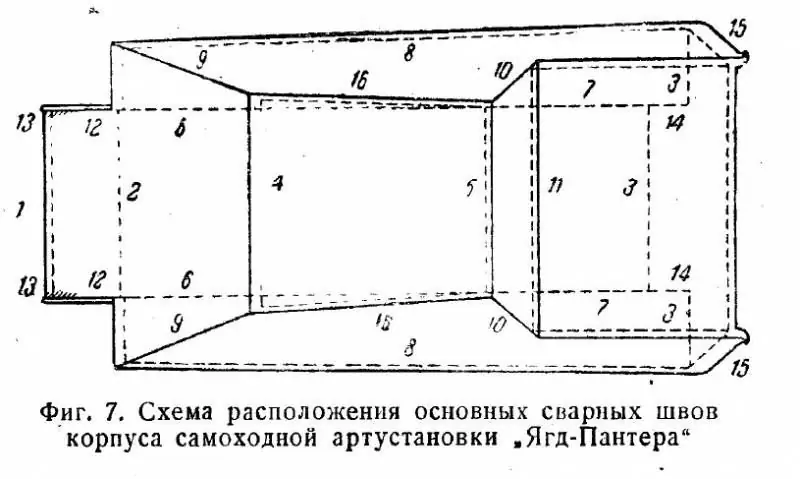
Almanlar, tank gövdelerinin kaynağını, ön çiviler olmadan büyük eğimlerde oldukça rahat koşullarda gerçekleştirdiler (bazı durumlarda, eklemin tüm uzunluğu boyunca hala 5 mm'lik bir elektrottan geçtiler). Tilt, bir şişte olduğu gibi, bir Alman tankının karkasının uzunlamasına eksen etrafında döndüğü bir yapıydı. Sürücü manuel veya elektrikliydi. Yüksek kesme doğruluğu nedeniyle, gövdenin rotator üzerine monte edilen parçaları arasındaki boşluklar (en azından savaşın ana döneminde) 3-4 mm'yi geçmedi. Bunun dışında çelik proses contaları kullanılmıştır. Uzun dikişler kaynakçılar tarafından birkaç küçük parçaya bölündü ve aynı anda tek yönde kaynaklandı. Kapatma dikişleri de iki kaynakçı tarafından senkronize olarak birbirine kaynaklanmıştır. Bu, çeliğin minimum sertleşme stresini ve en düzgün dağılımı sağladı. Alexander Volgin tarafından "Alman Menagerie Çerçevesi" malzemesinde dile getirilen efsanelerden birine göre, Üçüncü Reich'in bazı işletmelerindeki kaynakçıların maaşı parça başıydı - tankta biriken metal kütlesi için.
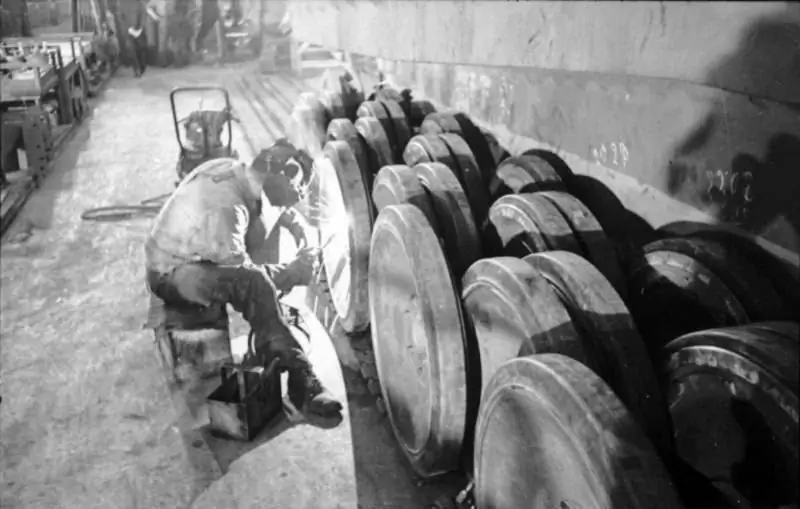
Alman tank endüstrisinde kaynak dikişlerinin kontrolü için herhangi bir özel kural hakkında konuşmaya gerek yok - X-ışını, manyetik kusur tespiti, ilkel delme yoktu. Ve dikişlerde çatlaklar vardı! 100 mm uzunluğa kadar ise taşlanır ve kaynak yapılır, daha fazla ise elektrik arkıyla eritilir ve kaynak yapılır. Aynı şeyi ana zırhta görsel olarak tespit edilen çatlaklar için de yaptılar. Bu arada, zamanla Almanlar, yeni elektrot bileşimleri nedeniyle kaynaklı dikişlerdeki çatlak oranını %30-40'tan %10-20'ye düşürmeyi başardılar. Ayrıca, östenitik ve ferrit elektrotlarla çok katmanlı kaynaklarda geçişlerin değiştirilmesi de kullanıldı.