Sovyet endüstriyel seçkinlerinin vatanseverliği, nihai sonuç için ortak sorumlulukla birleştirildi.
Endüstrilerarası etkileşim her zaman - hem Rus İmparatorluğu'nda hem de SSCB'de ve bugün - yerli sanayinin güçlü yönlerine ait değildi. Sözleşme yükümlülüklerinin değişmez ve neredeyse kutsal bir güce sahip olduğu ve sahip olduğu Almanya veya Amerika Birleşik Devletleri'nin aksine.
Örneğin, Rus metalürji uzmanları ve makine üreticileri arasındaki ilişkiyi ele alalım. 19. yüzyılın ikinci yarısında, yeni ulaşım mühendisliği fabrikaları ve tersaneler, Ural madencilerinden gerekli miktarda endüstriyel metal almadı. İkincisi, aynı kârın çok daha küçük hacimli pahalı çatı kaplama demiri tarafından sağlandığından, nispeten ucuz haddelenmiş ürünler üretmenin kârsız olduğunu düşündü. Araba aksları, motor milleri ve gemi kaplaması için eksik olan metalin yurt dışından satın alınması gerekiyordu. Sadece yüzyılın sonunda, sorun Belçikalı veya Fransız sanayiciler tarafından kurulan güney Rus metalurji tesisleri tarafından çözüldü. Urallarda Fransızlar da bir bitki inşa ettiler - Chusovskaya.
Görünüşe göre Sovyet döneminde bu tür kaprisler söz konusu değildi. Ayrıca 30'lu yıllarda inşa edilen metalurji tesisleri, ülkeye bir bütün olarak metal sağlamıştır. Bununla birlikte, makine üreticileri yeni karmaşık haddelenmiş ürün türlerini her talep ettiğinde, metalürji uzmanları yıllarca, hatta on yıllar boyunca bunlara hakim oldular.
departman feodalizmi
Uralvagonzavod'un tarihine dönelim. Zaten ilk projelerinde, tedarikçisi yakındaki Novo-Tagil Metalurji Fabrikası'na planlanan tasarım kapasitesi tasarım kapasitesine ulaştığı için dört dingilli arabaların altında katı haddelenmiş çelik jantlar kullanılması planlandı. Bununla birlikte, ikincisi metalurji departmanı tarafından inşa edildi ve tekerlekli haddehanenin yapımını ilk etapta değil 1938-1942'ye erteledi. Sonuç olarak, dava savaştan önce başlamadı. Ve savaştan sonra, metalürjistlerin tekerlek kiralaması pek ilgilenmedi. Sonuç: 50'li yılların ortalarına kadar Tagil arabaları fabrikadan çelik yerine kısa ömürlü dökme demir jantlarla çıktı. Bu, demiryolu işçilerine büyük kayıplar verdi, ancak başka seçenek yoktu: ya bu tür arabalar ya da hiçbiri.
Aynı şey, düşük alaşımlı çeliklerin vagon yapımında kullanılmaya başlanmasıyla da oldu. Tüm performans özelliklerini korurken, vagonların ölü ağırlığında gözle görülür bir azalma vaat ettiler. Uralvagonzavod'un tasarımcıları, 30'ların sonunda düşük alaşımlı metalden yapılmış arabalar tasarlamaya başladılar, ancak metalürji uzmanları, döküm parçaları için uygun haddelenmiş ürünler veya ferroalyajlar sağlamadığından, seri üretimleri yalnızca 50'lerin ikinci yarısında başladı.
Departman feodalizmi virüsünün makine üreticilerini etkilediği söylenmelidir. 1937 yazında, o zamanın kurumlar arası ilişkilerini karakterize eden ilginç bir hikaye yaşandı. Metalurji İşletmeleri Ana Müdürlüğü, Uralvagonzavod'a Novo-Tagil Fabrikasının yeni başlatılan bandaj değirmeni için beş bin ton boşluk siparişi gönderdi. Ulaştırma Mühendisliği Ana Müdürlüğü, alt bir işletmeye yapılan tecavüzden dolayı öfkelendi. Merkez Müdür Yardımcısı G. G.11 Temmuz'da Aleksandrov, GUMP ve Uralvagonzavod'a şu ifadeyi içeren bir mektup gönderdi: “Uralvagonzavod'da boş bir bandaj üretiminin organize edilmesi gibi önemli bir sorunun çözümünün bizim katılımımız olmadan gerçekleştirilmesi ve hatta daha fazlası için son derece şaşırdık. - Uralvagonzavod'a gönderilen kıyafetin bir kopyası bile bize gönderilmedi … Fabrikalarımıza sadece bizimle anlaşarak ve Glavtransmash aracılığıyla boşluk vermek için kesin bir prosedür oluşturmanızı rica ediyorum."
Sonuç olarak, metalurji uzmanları, iddiaya göre Uralvagonzavod'un açık ocaklı dükkanında yüksek kaliteli külçeleri dökmenin teknik imkansızlığı nedeniyle bandaj çeliği reddedildi. Bu arada, zaten 1936'da, burada eksenel bir boşluk ve 1937'de - sac haddeleme için külçeler döküldü. Bu nedenle, UVZ'den birkaç kilometre uzakta bulunan örtü değirmeni için külçelerin Vyksa ve Kuznetsk tesislerinden taşınması gerekiyordu. Ayrıca, kaliteleri arzu edilenden çok daha fazlasını bıraktı ve malzeme miktarları yetersizdi.
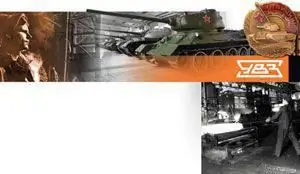
1938'de tarih tekerrür etti. UVZ külçelerinin ana tüketicisi, yıl sonunda bir yığın boşluk alan Molotof (yani Perm) Topçu Fabrikasıydı. Ve sadece birkaçı, kayıp metali iki veya iki buçuk bin kilometre boyunca ithal etmek zorunda kalan bandaj dükkanına gitti. Uralvagonzavodsk çeliğinin dağıtımındaki endüstri çıkarları açıkça üstün geldi.
Bölüm hastalığı da savunma sanayisini kurtarmadı. Sovyet tank inşa tarihi üzerine çok sayıda yayın, metalin, özellikle zırhın teslim edilmemesi nedeniyle prototiplerin inşasının veya seri üretimin konuşlandırılmasının nasıl ertelendiğine dair örneklerle doludur.
Ve bugün bile sektörel çıkarlar bir yere varmamış, sadece şekil değiştirmiştir. Yeni şekillendirilmiş haddelenmiş ürün formlarına yönelik talepler, fahiş fiyatlarla basitçe karşılanmaktadır. Koordineli bir politikadan bahsetmeye gerek yok. 2014-2015 döneminde ruble döviz kurunun çöküşünden sonra, metalürji şirketleri vagon fiyatlarını yüzde 30-60 oranında artırdı. Ve hemen fiyatları artan ekipman için makine üreticilerinden şikayet etmeye başladılar - sonuçta, makineler Rusya'da üretiliyor ve dolar kuruna bağlı değil.
Görünen o ki ülkemizde sektörler arası sorunların tek bir çaresi var: Kendi güçlerimiz tarafından çıkarılan cevherin önce metale, sonra bitmiş makinelere dönüştürüldüğü dikey olarak entegre sistemlerin oluşturulması.
savaş zamanı birliği
Bununla birlikte, tarihimizde endüstri çıkarlarının arka plana çekildiği kısa bir dönem vardır. Büyük Vatanseverlik Savaşı'ndan bahsediyoruz. O zamanlar Sovyet sanayi seçkinlerinin şüphesiz vatanseverliği, nihai sonuç için savunma üretiminde yer alan herkesin ortak sorumluluğu ile birleştirildi. Yani, zırhlı haddeleme tesisinin müdürü, eritilmiş ve haddelenmiş çeliğin hacminden değil, inşa edilen tank sayısından sorumluydu.
Bu yöndeki ana adım, NII-48 A. S.'nin direktörü Zavyalov tarafından atıldı. Savaşın ilk günlerinde, hükümete, enstitüye, ülkenin doğusundaki ilk zırhlı imalatında yer alan işletmelerde özel çelik ve zırhlı yapıların üretimi için teknolojiler tanıtması talimatını verme önerisiyle döndü. Araçlar. Temmuz ayı başlarında, NII-48'den uzman ekipler, en büyük 14 işletmenin teknolojik yeniden yapılandırılmasına başkanlık etti. Bunlar arasında Magnitogorsk ve Kuznetsk Metalurji Fabrikaları, Novo-Tagil ve Chusovka Metalurji Fabrikaları, Ural Ağır Makine İmalat Fabrikası, Gorki Krasnoye Sormovo, Stalingrad Traktör Fabrikası, Stalingrad Kızıl Ekim ve No. savaş öncesi tabu: Listede üç kişi komiserliğinin işletmeleri yer aldı.
Vatanseverlik ve departman egoizminin zorunlu olarak bastırılması, Sovyet metalurjisine, ne savaş öncesi ne de savaş sonrası dönemde benzeri görülmemiş savunma ürünleri geliştirme oranları sağladı. Birkaç ay içinde, ülkenin doğusunda (öncelikle Urallarda), ferromangan, ferrosilisyum, ferrokrom, ferrovanadyum ve diğer alaşımların üretimi düzenlendi, bunlar olmadan zırh çeliği elde etmek imkansızdı. Batı bölgelerinin kaybedilmesinden sonra, Chelyabinsk SSCB'deki tek ferroalyaj tesisi olarak kaldı. Üzerinde, kısa sürede, eritme iki buçuk kat arttı. 25 çeşit ürün üretildi, ancak bunların çoğu çeşitli ferrokrom türlerindendi. Ferromangan eritme, yüksek fırınlarda ve yalnızca Nizhniy Tagil ve Kushvinsky tesislerinin düşük tonajlı eski yüksek fırınlarında değil, aynı zamanda Magnitogorsk Combine'ın büyük bir modern fırınında da kuruldu. Tüm savaş öncesi fikirlerin aksine, ferrokrom 1941'in ikinci yarısında Nizhniy Tagil ve Serov fabrikalarının metalurjistleri tarafından yüksek fırınlarında eritildi ve SSCB Bilimler Akademisi'nin Ural şubesinden bilim adamları yeni bir oluşum yaratmada büyük yardım sağladılar. teknoloji. Daha sonra, Serov yüksek fırınlarında ferrosilikon eritme konusunda uzmanlaştı.
Savaştan önce Urallarda veya Batı Sibirya'da zırhlı kamplar yoktu, savaş bölgesindeki işletmelerden aceleyle transfer edilmeleri gerekiyordu.
1941 yazında, tahliye edilen ekipman hala yoldaydı. Ve sonra Magnitogorsk Combine N. A. Ryzhenko'nun baş tamircisi, zırhı çiçek açan bir değirmende yuvarlamayı önerdi. Büyük riske rağmen, fikir gerçekleştirildi. Ve Ekim ayında, Mariupol fabrikasından çıkarılan bir zırhlı kamp hizmete girdi. Sadece 54 günde toplandı. Savaş öncesi standartlara göre bu bir yıl sürdü.
Novo-Tagil fabrikası kampı Leningrad'dan aldı. Kabulü için hazırlıklar Temmuz ayında başladı, başlangıçta bandaj yerine monte edileceği varsayıldı. Bandaj kampı demonte edildi, ancak eski stoğun zırhlı kampı kurmak için yeterli olmadığı ve başka bir yere yerleştirilmesi gerektiği ortaya çıktı. Savaş, yakın zamana kadar imkansız olarak kabul edilen şeyi yapmak zorunda kaldı: sadece bir yıl önce, Nizhny Tagil'de entegre bir "yüksek hızlı" yöntemle endüstriyel inşaat yapma girişimleri, en iyi ihtimalle kısmi bir başarı elde etti ve 1941 yazında en fazla başarı elde etti. karmaşık inşaat operasyonu neredeyse mükemmeldi. 10 Eylül'de, ilk Tagil çelik sacı planlanandan bir ay önce haddelendi. Toplamda, yıl sonuna kadar, zırhın yaklaşık yüzde 60'ı dahil olmak üzere 13.650 ton sac metal elde edildi (değirmen karbon çeliği üzerinde test edildi ve Ekim - Aralık aylarında karbon çeliği zırh külçesi sıkıntısı ile haddelendi). Sonuç olarak, zaten Ocak 1942'de, Ural fabrikalarındaki aylık zırh plakası üretimi, savaş öncesi Sovyetler Birliği'nin tamamında altı ayı aştı.
Diğer az bilinen işletmelerde daha az şaşırtıcı olaylar yaşanmadı. Savaş sırasında, Zlatoust Metalurji Fabrikası, eritme ve haddelenmiş çelik hacmi açısından Magnitogorsk Kombine'den daha düşüktü, ancak ürün karışımında önemli ölçüde aştı - burada yaklaşık 300 derece alaşım ve karbon çeliği üretildi. Zlatoust'tan tedarik olmasaydı, başta tank motorları olmak üzere birçok silah türünün üretimi duracaktı.
Eski Ural fabrikaları, özellikle yüksek kaliteli çelikten küçük partilerin üretiminde vazgeçilmez olduğunu kanıtladı. Örneğin, kalibre edilmiş haddelenmiş ürünlerin ana üreticisi olan Serov Metallurgical'ın metali her Sovyet tankına yatırıldı. Nizhnesalda tesisi nikel demir ve çelik eritme işlemine geçti. Bu listeye sonsuza kadar devam edilebilir - savaş yıllarında, en az bir kubbenin olduğu her yerde silah sınıfı metal eritildi.
Otomatik kaynak için akılarla ilgili ilginç bir hikaye var. Savaşın öncesinde ve başında, işgalden sonra merkezi tedarikin tamamen durduğu Donbass işletmelerinden birinde eritildiler. 1941'in sonunda, Ukrayna SSR Bilimler Akademisi Elektrik Kaynak Enstitüsü çalışanları, Urallarda az çok kullanılabilir durumda bulunan yedek malzemeleri aramaya başladı. Ve onları Ashinsky metalurji tesisinin yüksek fırın cürufları şeklinde buldular. Sadece küçük iyileştirmeler gerekliydi: yüksek fırınlar cüruflarını manganez ile zenginleştirdi ve böylece onları tamamen uygun bir eritkene dönüştürdü. Test için gerekli ekipman Nizhny Tagil'den doğrudan Asha'ya getirildi.
Tank ve metalurji tesisleri arasındaki yerel işbirliği örnekleri çok açıklayıcıdır. Nizhniy Tagil Metalurji Fabrikası'nda kendi tesislerinin piyasaya sürülmesinden önce, Ural Tank Fabrikası No. 183'ün tank parçalarının ısıl işlemi gerçekleştirildi.
UTZ dökümhane işçilerinin başarılı çalışmaları, yüksek kaliteli ateşe dayanıklı çakmaktaşı tıkaçların üretimini kuran komşu Nizhniy Tagil havai fişek fabrikasının yardımıyla büyük ölçüde kolaylaştırıldı. Bu, şekillendirilmiş döküm için ağır zırh çeliği eriyiklerinin sorunsuz dökümünü mümkün kıldı.
1942-1945'te, UTZ'deki açık ocak fırınları esas olarak Novo-Tagil Metallurgical ve Nizhniy Tagil Kok Fabrikalarından gelen kok fırını ve yüksek fırın gazıyla çalıştı. Gaz boru hattı Şubat 1942'den beri faaliyette. 183 No'lu Fabrika'nın kendi gaz üretim istasyonu ihtiyacın yüzde 40'ından fazlasını karşılamıyordu.
Bazen bir sorunu çözmek için basit bir tavsiye yeterliydi. Yerel metalürjistlerden 1870'lerde geliştirilen küçük bir manganez madenine ilişkin bilgiler, tank paletlerinin dökümünü durdurmadan ferromangan teslimatlarının başlamasından birkaç hafta önce hayatta kalmasına yardımcı oldu.
Başka bir örnek: zırhlı çelik üretimi arttıkça, açık ocak atölyesi artık hava bombalarının başlıkları için metal eritme işine ayak uyduramadı. Dışarıdan almak mümkün değildi. Yönetmen Yu. E. Maksarev anılarında daha ileri olayların gidişatını hatırladı: “Şehir komitesindeki toplantılardan birindeyken, eski, hala Demidov fabrikasının müdürüyle tanıştım ve benden dökümü almasını istedim. bomba kafaları. Dedi ki: Çelik konusunda yardımcı olamam ama tavsiyeyle yardımcı olurum. Ve fabrikasına geldiğimde bana orta üflemeli bir buçuk tonluk Bessemer konvertör gösterdi. Bana çizimleri verdi ve iyi bir mekanize demir dökümhanemiz olduğunu bildiğini ve sizin dönüştürücülerinizin kaynak yapacağını söyledi” dedi. 8 Eylül 1942 tarihli fabrika siparişi, Bessemer bölümünün Griffin tekerlek dükkanındaki organizasyonda üç küçük dönüştürücünün (her biri bir buçuk ton metal) bu şekilde ortaya çıktı. 25 Eylül'e kadar, proje, sermaye inşaat yönetiminin tasarım ve teknoloji departmanı tarafından hazırlandı, baş mekanik departmanının uzmanları, hızlı bir şekilde dönüştürücüleri ve kazanları - sıvı demir depolama tanklarını kaynakladı. Bessemer departmanının test çalışması ve beş parça adından oluşan deneysel bir partinin dökümü 1942 Ekim-Kasım başında gerçekleşti. Seri üretim Kasım sonunda başladı.
Konunun sonunda: savaş zamanında metalurji uzmanları ve tank üreticilerinin işbirliği her iki yönde de hareket etti. Ural Tank Fabrikasının kurucuları, Novo-Tagil Metalurji Fabrikasının birçok yeni ünitesinin devreye alınmasına katıldı. Mayıs 1944'te, zırhlı kule döküm atölyesinde yüksek fırının onarımı için önemli sayıda astar plakası üretildi.
Ancak metalürjistlerin ana yardımcısı elbette Ural Ağır Makine İmalat Fabrikasıydı. 1942-1945 için UZTM sipariş defterleri, hem tank endüstrisinin ihtiyaçları hem de Halk Demir Metalurjisi Komiserliği'nin işletmeleri için metalurjik amaçlar için yedek parça ve cihazların üretimi ile ilgili belgelerle tam anlamıyla doludur. 1942 sonbaharında, metalurji tesisleri için ekipman üretimi için özel bir bölüm UZTM'de resmen restore edildi. "Bölüm 15" kodunu aldı ve tedarik atölyeleri ve gövde üretimi için müdür yardımcısına bağlıydı.
Sektörlerin kesiştiği noktada başarı
Metalurji uzmanları ve tank yapımcılarının işbirliği, abartısız gerçek bilimsel ve teknik atılımlar olarak adlandırılabilecek bir dizi teknolojinin yaratılmasına yol açmıştır.
Zırh çeliğini eritip levha haline getiren metalurji uzmanları, ürünlerini zırhlı gövde üretimine aktardılar. Burada metal, şablona göre karşılık gelen parçalara kesildi. "Otuz dört" üretiminde özellikle gövdenin iki parçası tarafından çok fazla sorun yaşandı: çamurluklar (yan eğimli taraf) ve dikey yan plaka. Her ikisi de uzundu, kenarları boyunca eğik kesikler olan genişlik şeritlerinde bile.
Fikir, doğal olarak, bitmiş parçalara eşit genişlikte bir ölçüm şeridi yuvarlamayı önerdi. İlk olarak 1941 yazında Mariupol fabrikasının zırhlı araçları tarafından formüle edildi. Deneme haddeleme için, iki kademeli zırh külçesinin gönderildiği Zaporizhstal'da bir slablama değirmeni seçtik. Ama sonra işe başlamak için zamanları yoktu: ilerleyen Alman birlikleri hem kademeleri hem de Zaporozhye'nin kendisini ele geçirdi.
1941-1942'nin başında, yeni fabrikalarda zırh üretiminin tahliyesi ve geliştirilmesi sırasında yeterli şerit yoktu. Ancak, Mayıs 1942'de, Demir Metalurji Halk Komiserliği, tekrar T-34 ve KV tankları için kiralama emri aldı. Görevin zor olduğu ortaya çıktı: genişlikteki toleranslar -2 / + 5 milimetreyi geçmemeli, parçanın toplam uzunluğu için hilal şekli (bükülme) 5 milimetre idi. Kaynak işlemi talaşlı veya alevli kesme yapılmadan yapılabilmesi için kenarlarda çatlak, gün batımı ve delaminasyona izin verilmemiştir.
Deneysel çalışmalar, Magnitogorsk ve Kuznetsk metalurji tesislerinin haddehanelerinde, ilk başta herhangi bir özel başarı olmaksızın eşzamanlı olarak başladı. KV tankları için parça kiralama kısa süre sonra terk edildi, ancak T-34 sonunda başarılı oldu. NII-48 G. A.'nın metalurji departmanı başkanından oluşan yazar ekibi, KMK L. E.'nin baş mühendisi Vinogradov ve aynı fabrikanın mühendisi S. E. "kenarda" yuvarlanma yöntemi. Ocak 1943'te, Şubat - 486, Mart - 1636 adet olmak üzere 280 şerit yayınlandı. Nisan ayında, gerekli tüm testlerden sonra, T-34 tanklarının tekerlek davlumbazları için ölçüm şeritlerinin brüt üretiminin geliştirilmesine başlandı. Başlangıçta, UZTM ve Ural Tank Fabrikasına ve daha sonra diğer fabrikalara - T-34 tank üreticileri - tedarik edildiler. Başlangıçta yüzde 9,2 olan hurda, Ekim 1943'te yüzde 2,5'e düştü ve standart altı şeritler daha küçük parçalar yapmak için kullanıldı.
Yeni teknolojinin tam ve doğru bir değerlendirmesi, 25 Aralık 1943 tarihli TsNII-48'in ilgili raporunda verilmiştir: “Temelde yeni bir “geniş zırhlı şeridi“kenarda”yuvarlamak için yeni bir yöntem geliştirildi, test edildi ve brüt üretime sunuldu SSCB'de ve yurtdışında yakın zamana kadar mümkün olmayan kabul edildi. T-34 tankının zırhlı gövdesinin bitmiş kısmının genişliğine sahip kalibre edilmiş (ölçülen) bir şerit elde etmek, NKTP fabrikalarının uzunlamasına kenarları kesmeden zırhlı parçaların üretimi için yeni bir yüksek performanslı teknoloji benimsemesini mümkün kıldı. T-34 tankının (çamurluklar) ana zırhlı parçalarından birine yeni yöntemin uygulanması sayesinde, onları keserken çok önemli bir zaman tasarrufu (yaklaşık% 36) sağlandı. 1000 gövde başına 8C zırh çeliğinden yüzde 15'e varan tasarruf ve 15.000 cbm oksijen tasarrufu sağlandı” dedi.
1943'ün sonunda, T-34 gövdesinin başka bir kısmı için bir ölçüm şeridinin yuvarlanmasında ustalaştı - yan dikey kısmı. Sadece bu buluşun yazarlarına 1943 için Stalin Ödülü verildiğini eklemek kalır.
Aynı 1943'te, Ukrayna Metal Enstitüsü laboratuvarının (PA Aleksandrov başkanlığındaki) ve Kuznetsk Metalurji Kombine ve Ural Tank Fabrikası işçilerinin ortak çabalarıyla, tedarik için üretimde özel bir periyodik haddelenmiş profil geliştirildi ve ustalaştı. "otuz dört" - dengeleyici eksenin kütle ve kritik parçaları. Periyodik profilin ilk deneysel partisi Aralık ayında KMK'da alındı, 1944'ün başında seri üretim başladı. Ekim ayına kadar, Ural Tank Fabrikası, UZTM'nin katıldığı yılın sonunda tamamen yeni bir boşluktan dengeleyici aks üretimine geçti. Sonuç olarak, dövme çekiçlerinin verimliliği yüzde 63 arttı ve parça kırılma sayısı azaldı.
Tank yapımcılarının başarılı çalışmaları, Novo-Tagil Metalurji Fabrikasının bandaj değirmeninin vagonları tarafından büyük ölçüde kolaylaştırıldı. 1942 baharından başlayarak, azaltılmış işleme payları olan haddelenmiş omuz askıları tedarik ettiler, 1943'te paylar tekrar azaltıldı. Yeni kesme aletiyle birlikte, bu, omuz askılarının kesinlikle programa göre ve fazla stres olmadan zaman alıcı soyma işlemini gerçekleştirmeyi mümkün kıldı. Nadir bir vaka: Tank Endüstrisi Halk Komiseri V. A. Malyshev, 28 Eylül 1943 tarihli emriyle Tagil metalurjicilerine özel şükranlarını ifade etmenin gerekli olduğunu düşündü.
Ve son olarak, son örnek: 1943'te, önce Chelyabinsk Kirov fabrikasında ve daha sonra diğer işletmelerde T-34 destek tanklarının jantları özel profilli haddelenmiş ürünlerden yapılmaya başlandı. Bu başarı, V. A. Malyshev'in emrinde de kaydedildi.
Kore'de ele geçirilen T-34-85 tankını inceleyen Amerikan şirketi "Chrysler" uzmanlarının, özellikle savaş aracının yapıldığı çelik boşlukların mükemmelliğine dikkat çektiğini eklemeye devam ediyor. Ve ayrıca, çoğu zaman ABD metalurji işletmelerinin ürünlerinden sayıca fazla oldukları gerçeği.