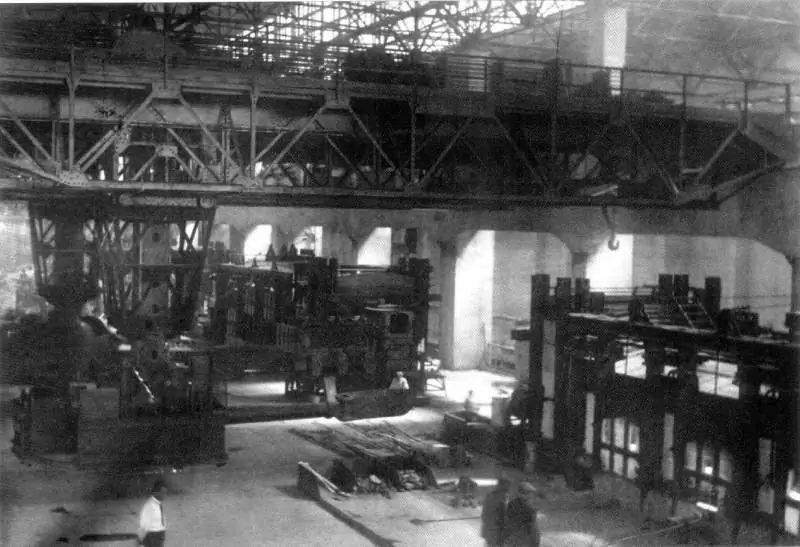
Stratejik kaynak
Savaş koşullarında askeri-sanayi kompleksi için yüksek kaliteli çelik üretimini abartmak zordur. Bu, orduların muharebe alanındaki başarısındaki en önemli faktörlerden biridir.
Bildiğiniz gibi, Krupp'un metalürji uzmanları, yüksek kaliteli silah kalitesinde çelik üretmeyi ilk öğrenenler arasındaydı.
Almanlar, 19. yüzyılın sonunda Thomas üretim sürecini benimsediler. Bu çelik eritme yöntemi, ürünün kalitesini otomatik olarak artıran fosfor safsızlıklarını cevherden çıkarmayı mümkün kıldı. Birinci Dünya Savaşı sırasında yüksek kaliteli zırh ve silah çeliği, genellikle Almanların savaş alanında üstünlüğünü sağladı.
Böyle bir üretimi organize etmek için fırınların iç yüzeylerini kaplayan yeni refrakter malzemeler gerekliydi. Almanlar, 2000 derecenin üzerindeki sıcaklıklara dayanarak, zamanları için en yeni manyezit refrakterlerini kullandılar. Daha yüksek refrakterliğe sahip bu tür maddeler, küçük alüminyum oksit karışımları ile magnezyum oksitlere dayanır.
20. yüzyılın başında, manyezit refrakterlerin seri üretimi için teknolojilere sahip ülkeler, yüksek kaliteli zırh ve silah namluları üretmeyi karşılayabilirdi. Bu, stratejik bir avantajla karşılaştırılabilir.
Yangına dayanıklılık açısından daha düşük, 1750 ila 1950 derece arasındaki sıcaklıklara dayanabilen yüksek derecede refrakter malzemelerdi. Bunlar dolomit ve yüksek alümina refrakterlerdir. Şamot, yarı asit, kuvars ve dinas refrakter malzemeleri 1610 ila 1750 derece arasındaki sıcaklıklara dayanabilir.
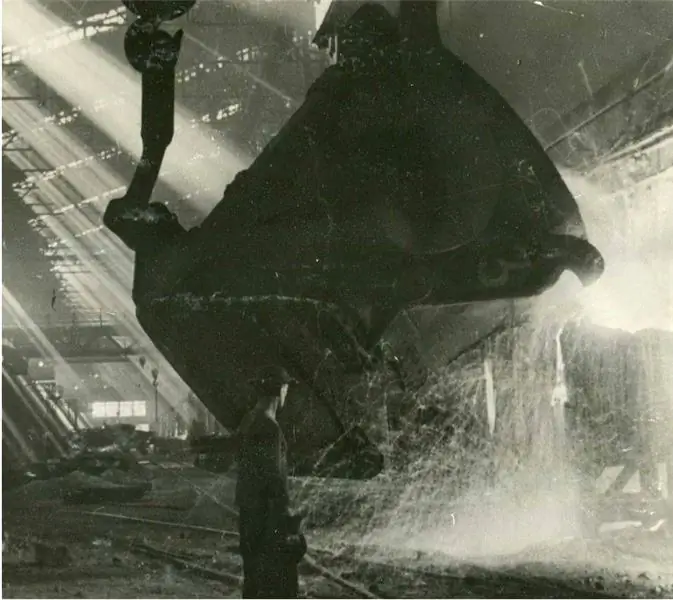
Bu arada, manyezit refrakter üretimi için teknolojiler ve alanlar ilk olarak 1900'de Rusya'da ortaya çıktı.
1905'te Satka manyezit refrakter tuğla, Liege'deki Dünya Endüstri Fuarı'nda altın madalya kazandı. Eşsiz bir manyezit yatağının bulunduğu Satka şehrinde Chelyabinsk yakınlarında üretildi.
Fabrikada refrakterlerin yapıldığı periklaz minerali yüksek kalitedeydi ve ek zenginleştirme gerektirmiyordu. Sonuç olarak, Satka'dan gelen manyezit refrakter, Yunanistan ve Avusturya'daki muadillerinden üstündü.
Boşluğu kapatmak
Satka'nın oldukça yüksek kaliteli manyezit tuğlasına rağmen, 30'lu yıllara kadar, Sovyet metalurjistlerinin ana refrakterleri kilden dinas malzemeleriydi. Doğal olarak, silah sınıfı çeliği eritmek için yüksek bir sıcaklık elde etmek işe yaramadı - açık ocak fırınlarının iç kaplaması ufalandı ve olağanüstü onarımlar gerektirdi.
Yeterli Satka tuğlası yoktu ve devrim sonrası dönemde ana üretim teknolojileri kayboldu.
Aynı zamanda, Avrupalılar öne geçti - örneğin, Avusturya Radex manyeziti mükemmel yangın direnci ile ayırt edildi.
Sovyetler Birliği bu malzemeyi satın aldı. Ancak bir üretim sırrı olmadan bir analog elde etmek imkansızdı. Bu sorun, Moskova Devlet Teknik Üniversitesi mezunu tarafından ele alındı. N. E. Bauman Alexey Petrovich Panarin. Magnet fabrikasında (eski adıyla Satka Combine), 1933'te Merkez Fabrika Laboratuvarı'nın başına geçti. Ve beş yıl sonra, açık ocak fırınları için periklaz-kromit veya kromomagnezit refrakterlerin seri üretimini başlattı.
Zlatoust Metalurji Fabrikasında ve Moskova Çekiç ve Orak'ta Panarin'in refrakterleri eski dinaların yerini aldı.
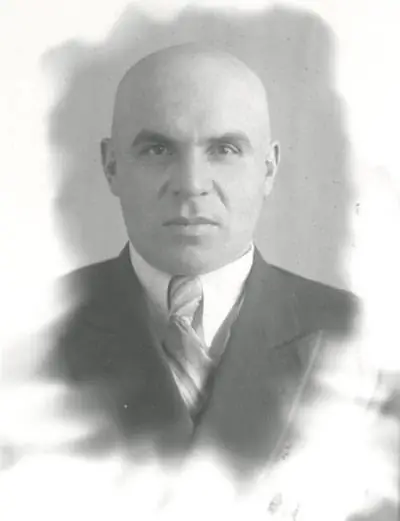
"Magnezit" laboratuvarında birkaç yıldır geliştirilen teknoloji, özel bir bileşim ve parçacık boyutundan oluşuyordu.
Daha önce tesis, manyezit ve krom demir cevherinden oluşan konvansiyonel krom-manyezit tuğlaları 50/50 oranında üretmekteydi. Panarin'in grubunun ortaya çıkardığı sır şu şekildeydi:
Sıradan bir manyezit yüküne minimum fraksiyon içeriği 0,5 mm'den az olan kaba granülometrik tanelerdeki kromit cevheri eklenirse, bu tür cevherin %10'luk bir ilavesiyle bile, tuğlanın termal kararlılığı keskin bir şekilde artar.
İri granülometrinin kromit cevheri ilavesi arttıkça, tuğlanın stabilitesi büyür ve belirli bir bileşen oranında maksimuma ulaşır.
Yeni refrakter için kromit Saranovskoye madeninde alındı ve Satka'da periklaz madenciliğine devam edildi.
Karşılaştırma için, sıradan bir "devrim öncesi" manyezit tuğla, Panarin'in yeniliğinden 5-6 kat daha az sıcaklıklara dayandı.
Kirovograd bakır eritme tesisinde, yankılı bir fırının çatısındaki krom-manyezit refrakter, 151 gün boyunca 1550 dereceye kadar sıcaklıklara dayandı. Önceden, bu tür fırınlardaki refrakterlerin her 20-30 günde bir değiştirilmesi gerekiyordu.
1941 yılına gelindiğinde, büyük ölçekli refrakterlerin üretimine hakim olundu ve bu da malzemelerin büyük çelik üretim fırınlarında 1800 dereceye kadar sıcaklıklarda kullanılmasını mümkün kıldı. Buna önemli bir katkı, refrakter malzemeyi fırınların çatılarına sabitlemek için yeni bir yöntem geliştiren "Magnezit" teknik direktörü Alexander Frenkel tarafından yapıldı.
Zafer için Refrakterler
1941'in sonunda, Magnitka metalürji uzmanları daha önce düşünülemez olanı başardılar - tarihte ilk kez, ana ağır açık ocak fırınlarında T-34 tankları için zırh çeliği eritme konusunda ustalaştılar.
Böyle önemli bir süreç için ana refrakter tedarikçisi Satka "Magnezit" idi. Fabrika işçilerinin üçte birinin cepheye çağrıldığı ve devletin planın gereğinden fazla yerine getirilmesini talep ettiği savaş zamanının zorluklarından bahsetmeye gerek yok. Bununla birlikte, tesis işini yapıyordu ve 1943'te Panarin
"Demir metalurjisi için yerel hammaddelerden yüksek derecede refrakter ürünlerin üretiminde ustalaşmak için"
Stalin Ödülü'ne layık görüldü.
1944'te, bu metalürji araştırmacısı, yüksek kaliteli manyezit tozu "Ekstra" üretimi için bir teknoloji geliştirecek. Bu yarı mamul ürün, elektrikli fırınlarda özellikle önemli zırhlı çelik üretiminde kullanılan preslenmiş bir refrakter hazırlamak için kullanıldı. Bu tür refrakterler için sıcaklık sınırı 2000 dereceye ulaştı.
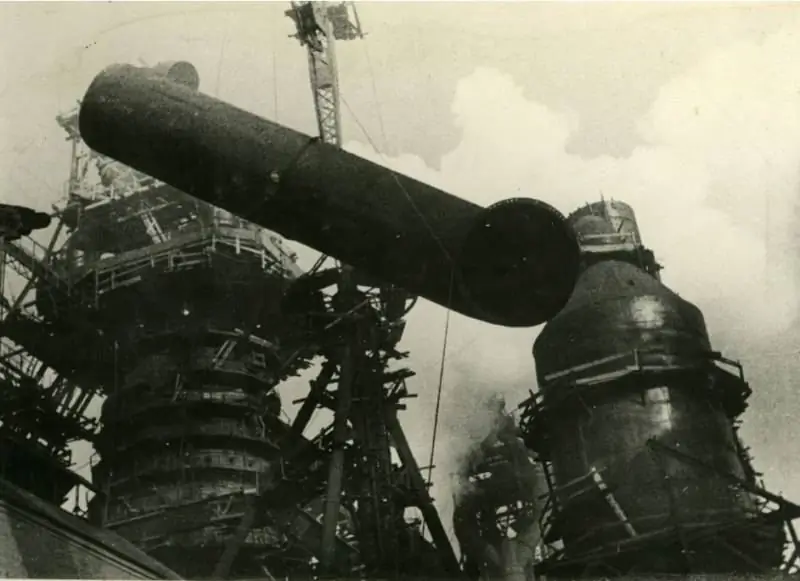
Ancak genel olarak başarılı bir Magnezit fabrikası örneğinin Sovyetler Birliği'nin tüm refrakter endüstrisini kapsadığını varsaymamak gerekir.
1941-1942'de neredeyse tüm ülkenin tank binasının boşaltıldığı Urallarda özellikle zor bir durum gelişti.
Magnitogorsk ve Novotagilsk metalurji tesisleri, zırh üretimine yeniden yönlendirildi ve Sverdlovsk Uralmash, Chelyabinsk "Tankograd" ve Nizhny Tagil tank fabrikası No. 183'e ürün tedarik etti. Aynı zamanda, metalurji tesisleri yerel hammaddelerden kendi refrakter üretimine sahipti..
Örneğin, Magnitka'daki dinas-şamot fabrikası yılda 65-70 bin ton tuğla üretti. Bu, kendi ihtiyaçları için bile yeterli değildi, diğer işletmelere tedarikten bahsetmiyorum bile.
İlk zorluklar, tank fabrikaları kendi ısıtma ve termik fırınlarını kurmaya başladığında ortaya çıktı. Ural metalurjisinde zaten zar zor yeterli refrakter vardı ve daha sonra tank fabrikalarının gövde üretimi, fırınları kaplamak için yüksek kaliteli malzemeler gerektiriyordu.
Burada herhangi bir kromomagnezit refrakterden söz edilmedi - bu malzeme yetersizdi ve hatta American Lend-Lease karşılığında ihraç edildi. En azından bir çok kaynakta bundan bahsediliyor. Ural tarihçileri, Panarin'in pahalı kromomagnezitinin, tank zırhı için kıt ferroalyajlar karşılığında yurtdışına gidebileceğini yazıyor. Ancak bunun henüz doğrudan bir kanıtı yok.
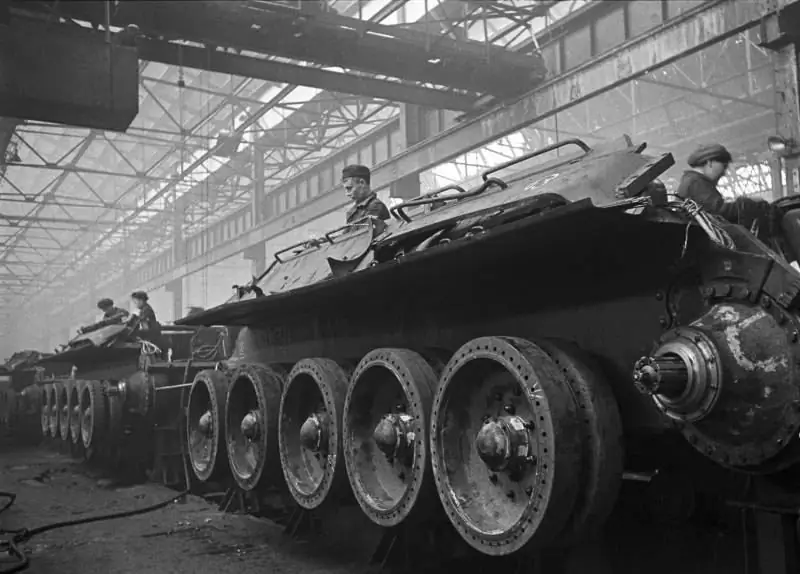
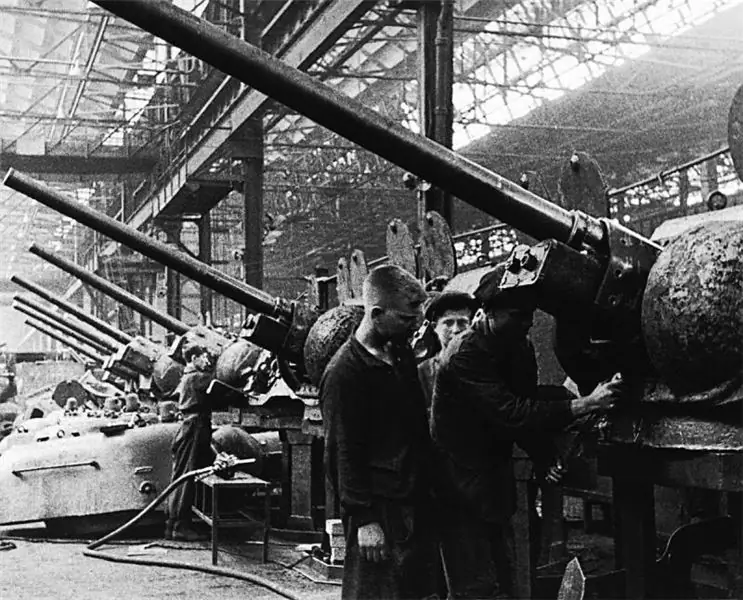
Tank fabrikaları çoğunlukla Pervouralsk fabrikası tarafından üretilen dinas refrakter malzemesine güveniyordu. Ancak, ilk olarak ayda sadece 12 bin ton üretildi ve ikincisi metalurji uzmanları aslan payını aldı.
Pervouralsk fabrikasındaki üretimin genişlemesi çok yavaş ilerledi. Ve 1942'nin ortalarında sadece 4 yeni fırın ortaya çıktı. Gerisi ya hazır değildi ya da genellikle sadece projelerde vardı.
Tank fabrikalarının açık ocak fırınları için refrakterler genellikle tam olarak ve yanlış zamanda değil, düşük kalitede geldi. Sadece Uralmash fırınlarının 1942'nin dördüncü çeyreğinde onarımı için 1035 ton ateşe dayanıklı tuğla gerekliydi ve sadece yaklaşık 827 ton alındı.
1943'te, genel olarak Uralmash'ın açık ocak dükkanı, onarım için refrakter eksikliği nedeniyle neredeyse durdu.
Savaş boyunca tedarik edilen refrakterlerin kalitesi arzulanan çok şey bıraktı. Normal koşullar altında açık ocak fırınının dinas tuğlası 400 ısıya dayanabiliyorsa, savaş zamanında 135 ısıyı geçmedi. Ve Mart 1943'e kadar bu parametre 30-40 ısıya düştü.
Bu durum, bir kaynağın (bu durumda, refrakter) eksikliğinin tüm savunma sanayisinin çalışmalarını nasıl ciddi şekilde yavaşlatabileceğini açıkça göstermektedir. Tarih bilimlerinin adayı Nikita Melnikov'un eserlerinde yazdığı gibi, Mart 1943'te Uralmash'ın üç açık ocak fırını hala durdu ve tam bir onarım çalışması gerçekleştirdi. 2346 ton dina, 580 ton şamot ve 86 ton kıt manyezit aldı.
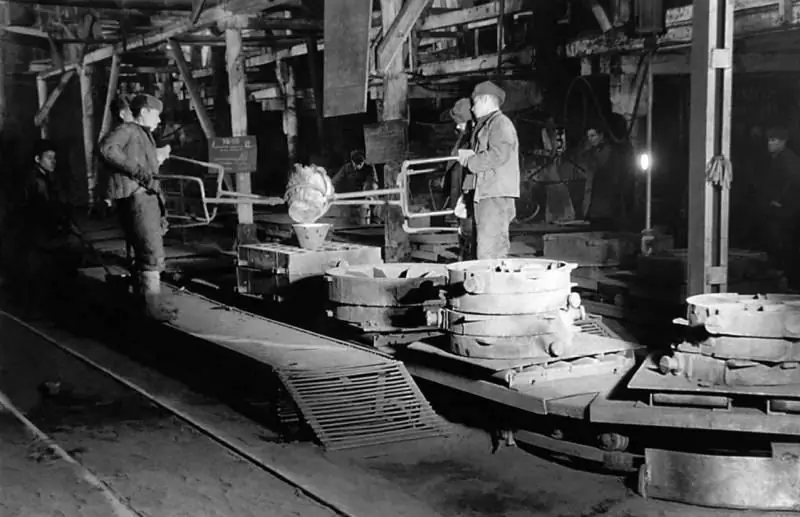
1942'nin ortalarında, 183 No'lu tank fabrikasında durum benzer şekilde gelişiyordu - çelik üretimi mekanik montajın gerisinde kaldı. Ve T-34 gövdelerini Uralmash'tan "ithal etmek" zorunda kaldık.
Sebeplerden biri, 1942 baharında sınırlarında çalışan açık ocak fırınlarının onarımı için refrakter eksikliğiydi. Sonuç olarak, sonbaharda 6 açık ocak fırından sadece 2'si faaliyetteydi, eritme hacimleri sadece 1943'ün ikinci yarısında restore edildi.
Büyük Vatanseverlik Savaşı sırasında Sovyet savunma kompleksinin yapısındaki refrakterlerin durumu, ülkenin arkasındaki durumun karmaşıklığını açıkça göstermektedir.
Genel olarak, en yüksek teknoloji ürünü olmayan kronik bir eksiklik, zırhlı araçların üretim hızını doğrudan etkiledi.